In industrial and urban environments, the weight of mechanical plastic parts, especially large ones, can pose significant challenges: difficult handling, high transport costs, and constraints related to installation, particularly at heights or on facades. To address these challenges, reducing weight becomes a top priority, without compromising rigidity and durability.
In this article, we explore two key steps to effectively reduce the weight of large mechanical plastic parts: choosing the right materials and implementing ingenious design solutions.
First Step to Reduce Weight: Material Selection
Selecting the right materials is a critical decision to optimize weight while maintaining mechanical performance. Here is a comparison of the densities of commonly used materials:
Material | Density (g/cm³) |
Aluminum | ~2.70 |
Plastic (ABS) | ~1.05 |
Steel | ~7.85 |
Wood (Oak) | ~0.90 |
Paper/Cardboard | ~0.70 |
Why Choose Plastic for Templates, Containers, Front Panels, or Mounting Parts?
- Lightweight: Technical plastics such as ABS, PC, or PMMA offer an optimal combination of low density and mechanical strength.
- Versatility: They allow customization in terms of shape, thickness, and finish.
- Durability: When combined with eco-friendly practices, such as using recycled plastics, they also reduce environmental impact.
The choice of material is therefore a fundamental step for any project aimed at minimizing the weight of large mechanical plastic parts.
Second Step to Reduce Weight: Ingenious Design Solutions
Once the material is selected, design becomes key to maximizing weight savings while maintaining rigidity. Here are some solutions implemented by LTP:
1. Hollow Walls via Folding
Creating hollow walls using folding techniques reduces the amount of material used while reinforcing the structure. These walls act as “boxes,” increasing rigidity with less weight.
2. Lightweight Structural Elements: Targeted Material Reduction
Certain areas, less mechanically stressed, can be lightened through strategic cuts or thinning. For example:
- Cross Reinforcements: Distribute loads optimally while removing material from the center.
- Functional Perforations: Targeted weight reduction while maintaining structural integrity.
3. Integrated Ribbing
Ribs or longitudinal reinforcements make it possible to reduce the overall wall thickness while retaining the necessary rigidity to withstand loads.
4. Geometry Optimization
Clever design, such as rounded corners or sloped surfaces, can reduce overall mass by avoiding unnecessary areas of extra thickness.
Case Study: A Mechanical Plastic Part for Urban Applications
A client wanted to install large rectangular mechanical plastic parts for an urban greening project on facades. Challenges included:
- Reducing weight to minimize stress on the facade structure.
- Ensuring sufficient rigidity to support the weight of the substrate and plants.
- Minimizing transport and installation costs.
Solution provided by LTP:
- Material Selection: Use of recycled ABS to ensure lightness and durability.
- Creation of Hollow Walls: To lighten the parts while increasing strength.
- Use of Integrated Ribbing: To distribute loads optimally.
Result: a 30% weight reduction compared to a conventional design, facilitating installation while meeting budget constraints.
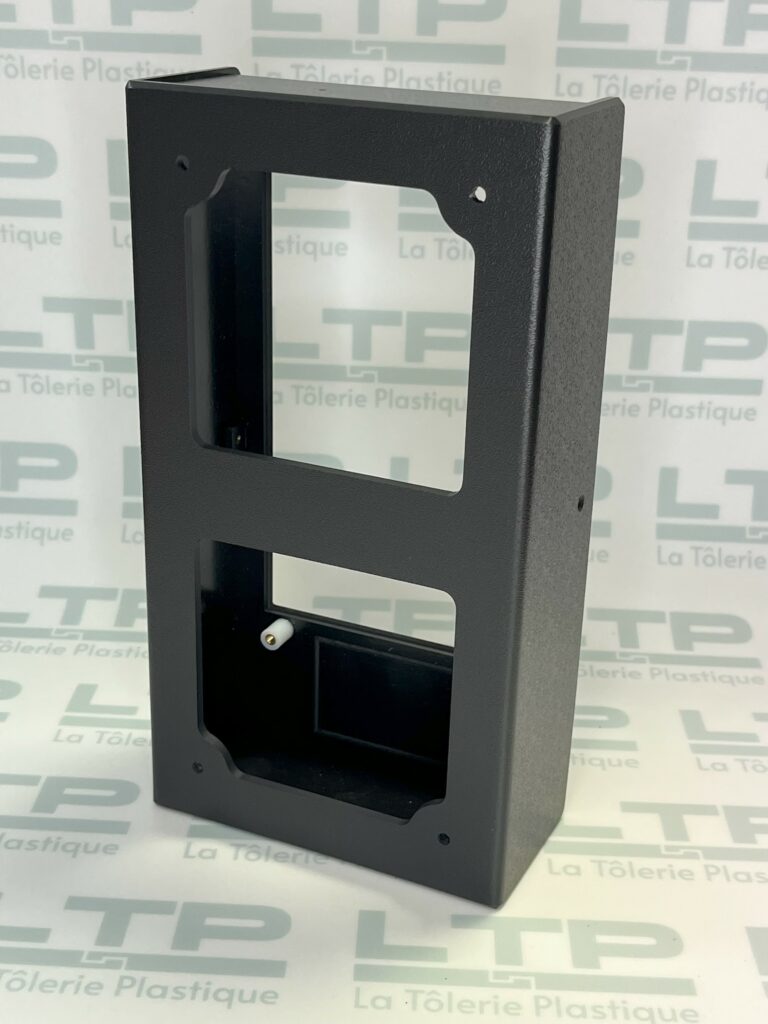
Why Choose LTP?
With over 30 years of expertise in custom manufacturing of plastic parts, LTP offers innovative, project-specific solutions. Whether for industrial or urban applications, we optimize every step of the design process to ensure lightness, rigidity, and durability.
Contact us today to discuss your project and discover our custom weight reduction solutions.
Phone: 0033 (0)2 35 54 63 40 | Email: sales@ltp.fr