Designing enclosures for electronic devices such as spectrometers requires close attention to thermal resistance, safety, and compliance with strict standards.
In particular, the UL746C standard, which governs plastic materials used in high-temperature devices, sets essential technical requirements.
Engineers and project managers in industrial design must therefore find a solution that combines performance, safety, and flexibility, without incurring high production costs and lead times. This is where Enclosure Technology in, offering bespoke solutions without the need for specific moulds.
What is a Spectrometer and How Does It Work?
A spectrometer is a measuring instrument used to analyse light. It breaks light down into its different wavelengths, allowing the identification of elements present in a sample. The basic principle is the interaction of light with matter:WikipediaWavelength
- Light Source: The spectrometer emits light directed at the sample.
- Interaction with the Sample: The light interacts with the sample, which may result in absorption, reflection, or transmission of specific wavelengths.Wikipedia
- Dispersive Device: The modified light passes through a prism or diffraction grating which separates it into different wavelengths.Les Sherpas
- Detector: The different wavelengths are then detected, usually by an electronic sensor, allowing a characteristic light spectrum of the sample to be obtained.
This process provides detailed information about the sample’s composition, as each element or compound has a unique spectrum. A sample could be aluminium, for example, where one wants to determine its alloy composition.
Why Is It Important to Comply with Standards for Spectrometers?
Spectrometers are used in sensitive applications where measurement accuracy and reliability are crucial. Complying with strict standards ensures that instruments deliver consistent and reproducible results. For instance, the UL746C standard outlines requirements for plastics used in devices operating at high temperatures. This ensures that the spectrometer’s components can withstand specific thermal conditions without degrading, which is vital for maintaining measurement accuracy and device safety.
The Challenges of Plastic Electronic Enclosures
Plastic enclosures for spectrometers must meet stringent criteria, especially regarding thermal resistance. Spectrometers may operate at temperatures of up to 150°C, requiring plastic materials that can withstand these conditions. The UL746C standard is therefore essential to ensure the enclosure delivers reliable and safe performance in demanding environments.
In addition to thermal resistance, an electronic enclosure must meet fire safety requirements by being flame-retardant. Plastics compliant with UL94 offer crucial fire resistance properties that protect sensitive electronic components at high temperatures. These safety features are vital for ensuring both performance and safety under extreme conditions.
LTP: An Innovative and Flexible Solution
LTP’s solution meets these technical requirements without the limitations of mould-based manufacturing. This process offers many advantages for producing plastic electronic enclosures, especially for small and medium-sized production runs such as those required for spectrometers.
No investment in a specific mould: This technology avoids the costs associated with creating and managing moulds, making it ideal for small production runs or prototypes.
Flexibility and customisation : Each project is unique, and the bespoke manufacturing of enclosures allows perfect adaptation of shape, size, and finish to each specific need. Whether integrating additional features like ventilation or providing customised aesthetic finishes (painting, marking), Tôlerie Plastique offers a fully tailored solution.
Short lead times: Enclosure technology reduces manufacturing time to 6 weeks, offering optimal responsiveness for time-sensitive projects.
Case Study: Enclosure for Spectrometer
Let’s take the example of a high-precision spectrometer project. The client required an enclosure capable of withstanding high temperatures, ensuring electronic component safety, and meeting UL746C standards. Thanks to LTP, the enclosure was manufactured without a specific mould, allowing fast and cost-effective production. The materials used met thermal resistance requirements, and customised finishes were applied to enhance the enclosure’s visual appearance. The result? A standards-compliant enclosure, produced quickly and affordably, while meeting the client’s technical requirements.
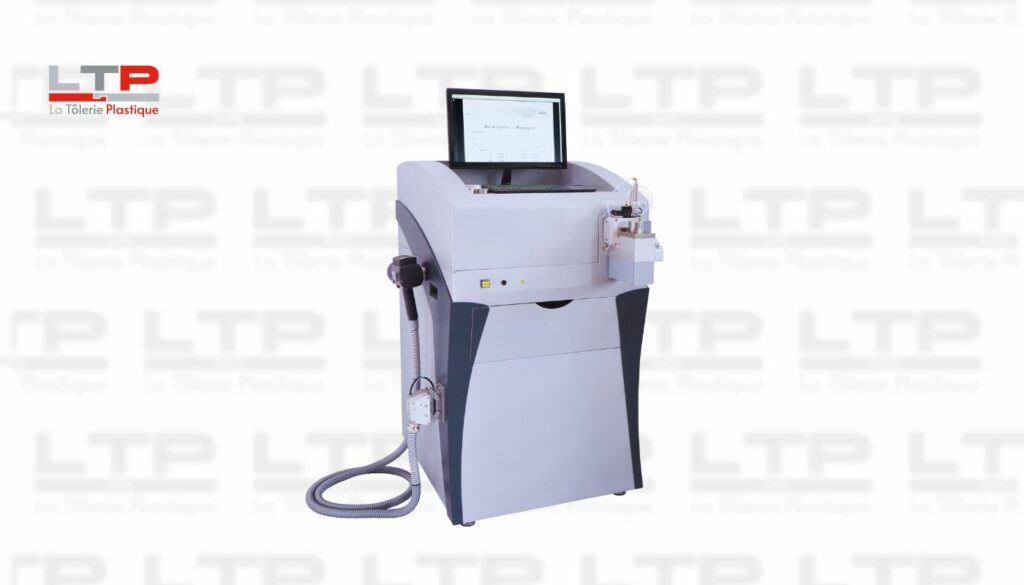
Why Choose LTP?
LTP stands out for its ability to meet the specific needs of electronic enclosure design projects, whether for small or medium production runs. Thanks to its mould-free process, LTP offers cost-effective and rapid solutions while guaranteeing optimal performance and extensive customisation. Additionally, with expertise in manufacturing flame-retardant and high-temperature-resistant enclosures, LTP ensures full compliance with standards such as UL746C.
If you are an engineer or project manager looking for a fast, flexible, and bespoke solution for your electronic enclosures, LTP is the partner you need.
📞 Contact us today to discuss your bespoke enclosure requirements and discover our innovative solutions.
📞 Phone: 0033 (0)2 35 54 63 40 | 📧 Email: sales@ltp.fr