LTP has been manufacturing plastic electronic enclosures since 1985, using a reliable and not very widespread technology invented by the company’s founder: “tôlerie plastique” (plastics sheet processing).
This is a no tooling process requiring no special mould, enabling us to manufacture customized plastic casings in small and medium-sized runs.
Adapted to the needs and constraints of our customers, they are produced in our workshops in Octeville-sur-Mer, near Le Havre, within short lead times.
Fully customizable, our enclosures, housings and parts are suitable for a wide range of sectors, including industry, beauty and healthcare.
They can be used in laboratories, for example, to dress and protect medical equipment.
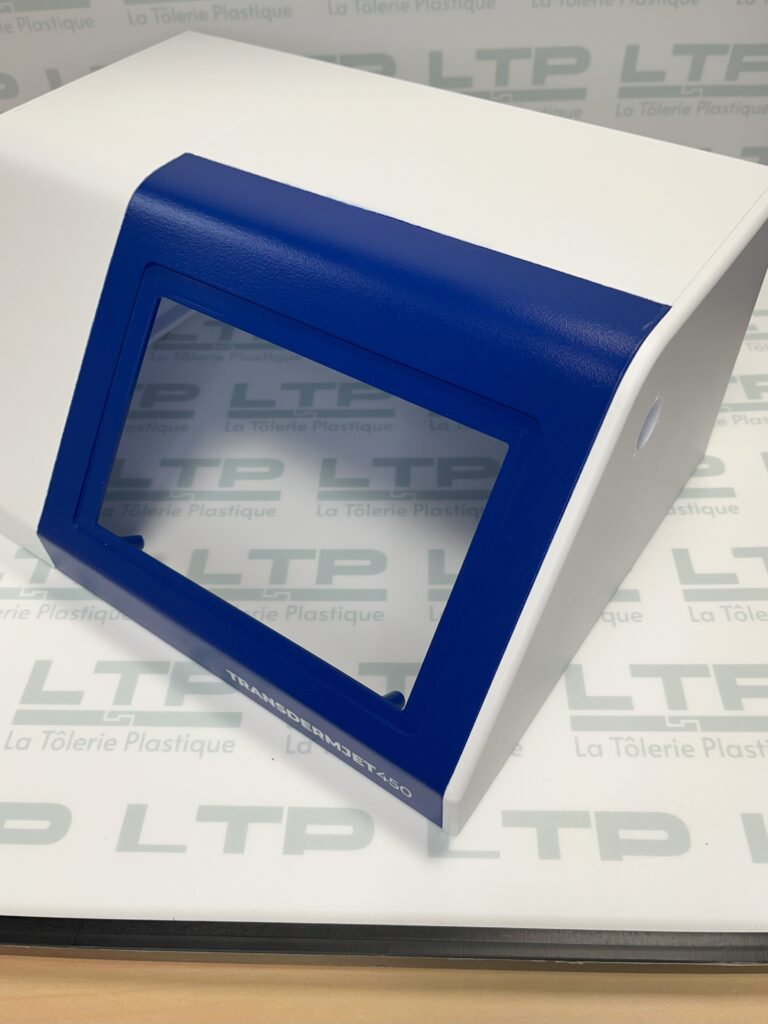
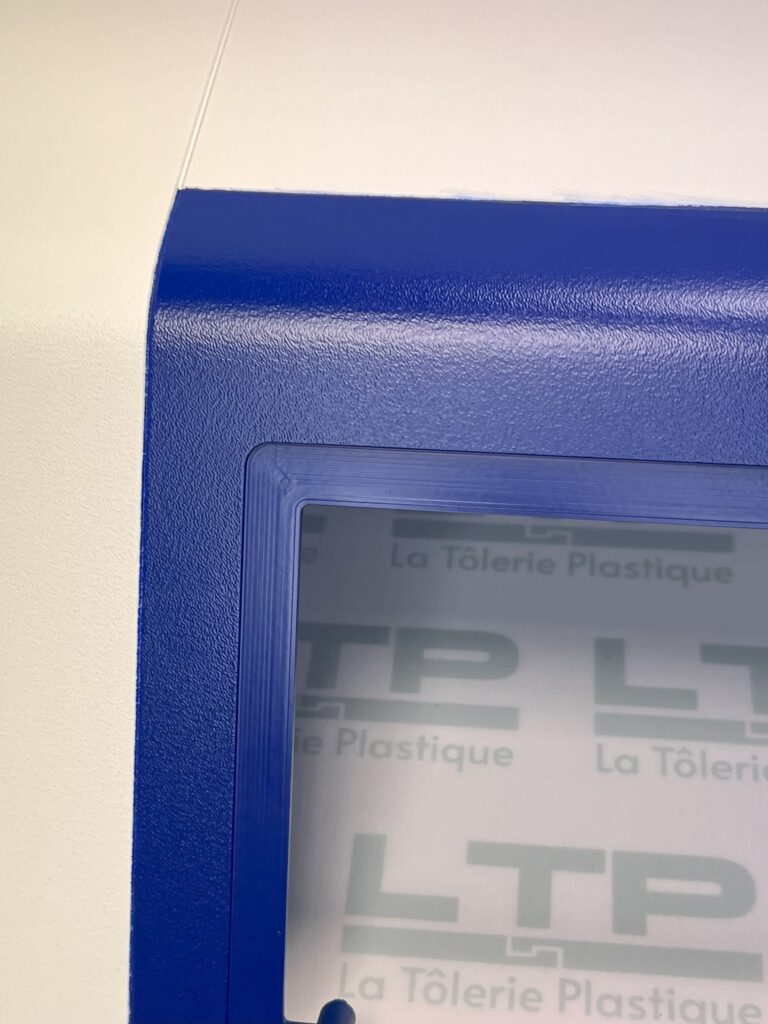
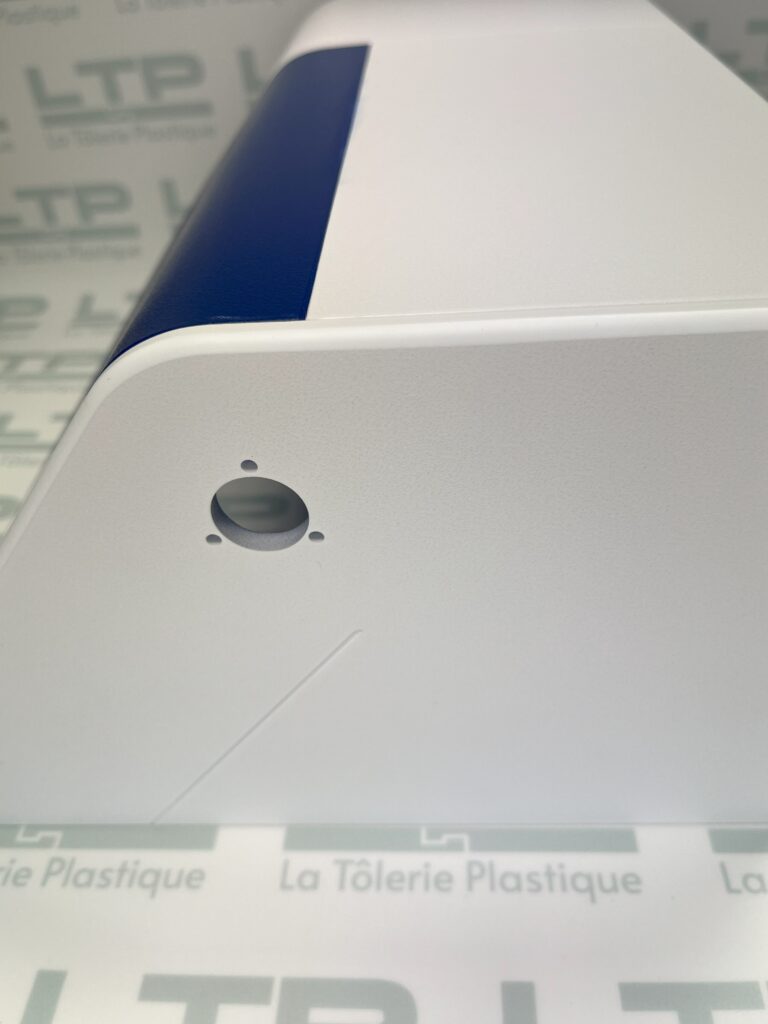
An atypical process for small and medium production runs
Plastic sheet processing offers many advantages for both the manufacturer and its customers.
These include:
- Possibility of a 100% made-to-measure product, with the technical specifications and finishes requested, and no size constraints
- No need to invest in moulds that would be uneconomical for small and medium production runs.
- Design and aesthetics ;
- Rapid industrialization process (development phase, design, prototype and first series production)
- Flexibility to change design, size or customization, quickly and at no extra cost.
Application example for a laboratory medical device
LTP has been mastering the art of plastic sheet processing working for almost 40 years, producing around 200,000 housings and enclosures a year.
For example, an OEM of laboratory devices needed a custom hood-shaped casing that could be modified between production runs. As the quantity to be produced was small – around 20 parts a year for several years – the LTP technology was the only cost-effective process. Investing in a mould would have been far too costly for this customer. As a result, we were able to offer a solution in line with the customer’s requirements and environment ( laboratory use): a customized cover with copper shielding and painting with a highly resistant varnish.
What’s more, every stage in the production of a plastic electronic enclosure is carried out by our own team, in our own workshops. This means we can provide our customers with complete support, and keep manufacturing times and costs under control.
If you’d like to find out more about plastic sheet metal work, please contact us. We’ll be happy to give you all the information you need, and to send you a customized quotation for your project.
LTP, your partner for custom enclosures, housings and plastic parts with precise, durable marking
For technicians and engineers aspiring to turn their electronic device into a commercial success, the TOLERIE PLASTIQUE process offers a perfect solution between 3D printing and injection molding. Our NO TOOLING plastics process has the flexibility of 3D printing and guarantees the reliability of injection molding.
As a designer and manufacturer, we offer you a :
- No special moulds required, adapted to your needs,
- Flexibility for all modifications, without constraints,
- No major initial investment required,
- 100% adapted to your target and application.
Start your project with LTP today: Request a quotation
Come and see our showroom and production facilities: Google Maps
What do you think of this information? Tell us what you think:
Would you like to find out more about this process? : Schedule an exclusive Teams Discovery Session for your teams; live in 30mins!
Contact us now : Form and contact details for our company (ltp.fr)