In the realm of industrial product development, the choice of marking techniques on plastic enclosures is crucial. For technicians and engineers in R & D departments this is a significant question: When should one opt for engraving instead of screen printing? The answer lies in the specific advantages and technical details that only engraving can offer.
Precision and Durability: The Key Advantages of Engraving
Engraving allows for fine and enduring markings crucial for technical information or identifications. This method is highly recommended by manufacturers of plastic enclosures who aim to provide their customers with long-lasting readability, even under demanding conditions for their electronic devices.
The Fundamental Difference from Screen Printing
Screen printing, while frequently used and cost-effective for monochromatic markings in large quantities, can wear off or fade over time, particularly in challenging industrial environments. Choosing engraving involves directly milling the marking into the material using a CNC engraver. The minimum processing width is comparable to text in Arial font size 8.
Marking of
- Text
- Logos
- Pictograms
- lettering
on ABS, PVC, PMMA, or polycarbonate panels ensures better resistance against abrasion, chemicals, and weathering. This property is critical for devices in industries such as general electronics or industrial applications.
Other Marking Techniques
Apart from engraving and screen printing, there are other marking methods presented on the “Plastic Printing” page:
- Digital printing is ideal for complex and multicoloured designs, offering great design flexibility.
- Labelling (Lexan) allows for identification at the end of production (CE marking, serial numbers).
- Pad printing works well for irregular or textured surfaces.
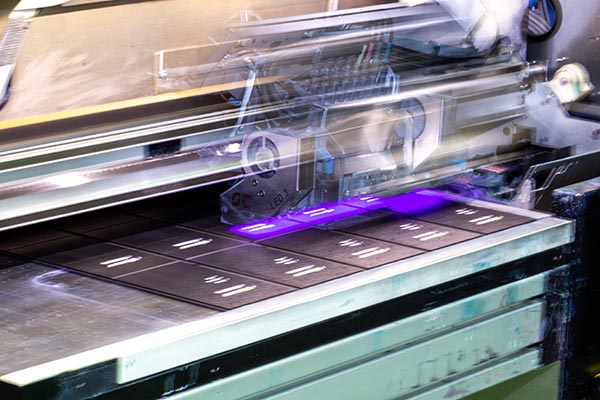
These techniques, though effective for specific applications, cannot compete with the durability and resistance of engraving.
Project Example with Engraved Marking
As a manufacturer of plastic enclosures, LTP understands the importance of engraving to offer personalised, high-quality, and abrasion-resistant solutions. One such challenge was met for project DT23050010, based on the pre-designed model Wall Enclosure ElectroniCase EC10-260-34.
- Construction without specific tooling: The enclosure consists of 3 basic elements (L and U shapes).
- Material: White ABS (Acrylonitrile-Butadiene-Styrene) sheet material, thickness 3mm, 2mm.
- Fixing elements for integrating/mounting electronic components:
- 1x Spacer dome (metric thread size M5, height 15mm) with a threaded insert (brass, metric thread size M3 height 4mm).2x Spacer domes (metric thread size M3 height 12mm).2x Collar-insert screws (metric thread size M2 height 2mm under the head).
- 4x Spacer domes with threaded insert for locking the enclosure (M4).
Upon the customer’s request, this enclosure was engraved with the Euro (€) symbol.
In addition to clear identification, engraving contributes to the aesthetics and functionality of the products, an advantage that will enhance the commercial success of your device.
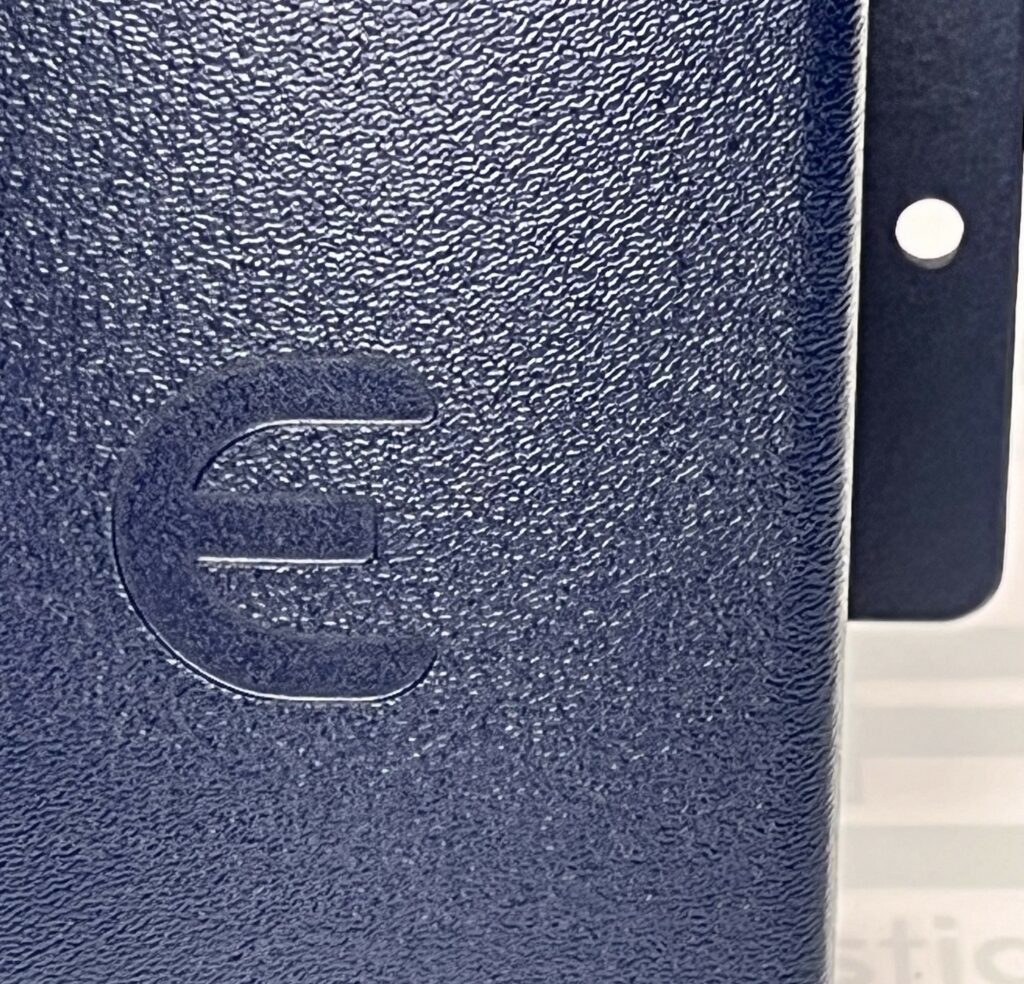
LTP, Your Partner for Custom Cases, Covers, and Plastic Parts with Precise and Durable Marking
For technicians and engineers looking to make their electronic device a commercial success, the process of sheet plastic bending offers a perfect solution between 3D printing and injection moulding. As a developer and manufacturer, we offer you clear values:
- Flexibility for all changes without limitations,
- Without significant initial investments,
- Without specific tooling and tailored to your technical requirements,
- 100% customized for your target audience and application.
Start your project with LTP today: Request a quote!